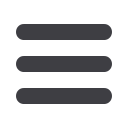
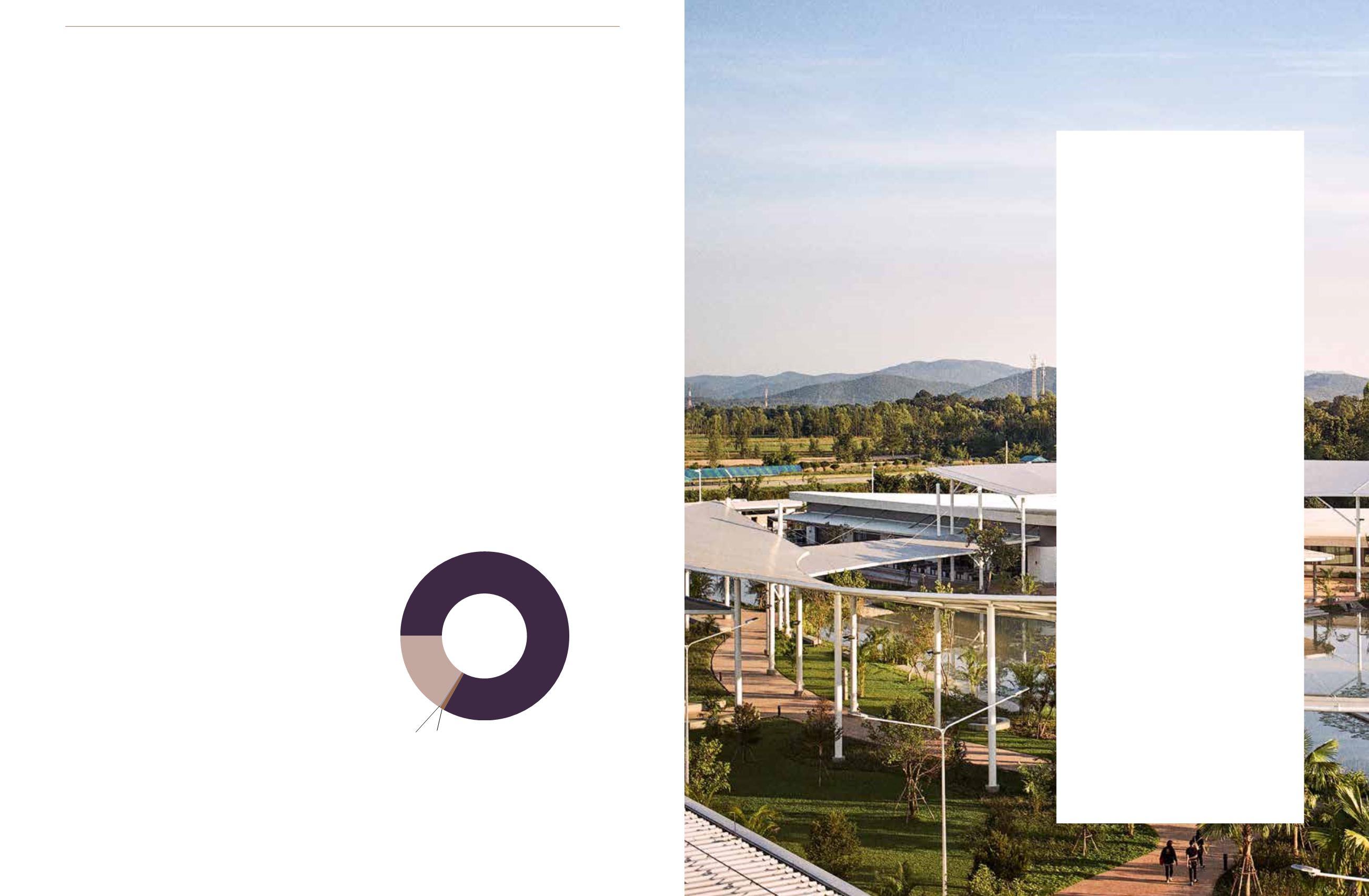
PANDORA ETHICS REPORT 2016
18
Our new LEED certified facilities have a clear focus on
water recycling, and we expect to improve our future water
consumption and recycling significantly.
Waste
The crafting of our jewellery generates four main types of
process waste: gypsum, glass, rubber and wax. Gypsum
waste is recycled in the construction sector, glass waste is
recycled into glass tiles, rubber waste is used as fuel by the
cement industry and, finally, wax waste is used in the
casting process by a figurine manufacturer. Some categories
are sold and others we pay to have recycled, as in the case
of gypsum where PANDORA pays for the transportation to
the vendor.
In 2015, these four main types of waste reached an
impressive result: 100% reuse or recycling, making the total
reuse or recycling of our crafting waste 83%. In 2016, we
were able to continue the trend with 100% recycling of our
main types of waste and a total recycling of 86%.
Find more detailed data on waste on
pandoragroup.com/csrMAN-MADE STONES
We gain many ethical advantages by predominantly using
man-made stones in our collections. The origin of man-made
stones is fully traceable and the ability to grow stones with
fewer quality variations considerably reduces material waste.
In a recent study carried out for PANDORA, the environmental
cost of man-made cubic zirconia stones compared to mined
diamonds is estimated to be decreased by more than 99%
when it comes to greenhouse gas emissions and air pollutants.
CRAFTING
PANDORA experienced a sharp increase in demand and
produced approximately 106 million pieces of jewellery in-
house in 2016. At the same time, the greater complexity and
intricacy of our jewellery designs have made it challenging
to simultaneously reduce our energy and water consumption
at our crafting facilities. With the new Leadership in Energy
and Environment (LEED) certified crafting facility in northern
Thailand and another LEED certified crafting facility currently
under construction in Bangkok, we expect to be able to
significantly improve our environmental performance in the
years to come.
Energy
PANDORA Production Thailand (PPT) is by far our most
energy-consuming entity. The amount of energy used here
increased from 29,472 MWh in 2015 to 35,907 in 2016.
The rise in energy consumption reflects the increase in
crafting complexity and the number of pieces of jewellery
produced. Besides the state-of-the-art burnout ovens used
in the crafting process, the extensive use of chillers to ensure
a cool and comfortable working environment throughout
our facilities consumes a considerable amount of energy.
Ovens and chillers put together account for approximately
40% of energy consumption. We expect the LEED-certified
facilities will significantly optimise the use of energy going
forward, plus contribute with solar power, and we look
forward to the future results.
Water
As a result of our growth and the increased complexity in
our jewellery designs, our water consumption at PPT
increased from 482,500 m
3
in 2015 to 584,108 m
3
in 2016.
In 2016, we invested in additional on-site waste water
treatment at our Bangkok facilities, drastically improving the
quality of waste water. The disposal of waste water is subject
to control by both our own SHE team and local authorities,
and is audited by external experts as a final check.
86% Reused/
recycled waste
14%
General
waste
0.1%
Hazardous
waste
0.5%
Industrial
waste
CRAFTING WASTE
BUILDING
FOR A GREENER
FUTURE
At PANDORA, we constantly strive to minimise our
impacts on the planet, and we have taken great strides
to ensure we can be environmentally friendly in
various ways, every day. In 2016, we opened a new,
highly modernised crafting facility in Lamphun in
Northern Thailand. Awarded the Leadership in Energy
and Environmental Design (LEED) certificate, the
new green building meets the highest demands
regarding CSR and sustainability, placing PANDORA
in a league of its own in the jewellery industry.
The construction process itself aims for high
sustainable standards. In order to minimise transport
emissions, most of the building materials originates
from an area within 800 km from the construction site,
30% of construction materials are made of recycled
content, and 75% of the construction waste was
diverted to recycling facilities.
The new facility provides an inspiring and healthy
working environment for our colleagues. Due to its
many impressive sustainability features, water and
energy usage is lower than ever: A reduction of 45%
in water consumption is possible due to a specially
designed water management system, and innovative
air conditioning and ventilation systems help reduce
ventilation energy losses by up to 80%. At the same
time, solar panels on the roof of the main crafting
facility generates electricity equivalent to 14% of the
total energy consumption of the facility corresponding
to 700 Thai households.
And it doesn’t stop there. Another sustainable, state-
of-the-art crafting facility is due for completion in
2018 at our site in Bangkok, Thailand. Additionally,
in Copenhagen, Denmark, the new PANDORA
Global Office, which we moved into in 2016, are
LEED-certified in the gold category. Here, energy
consumption is powered by windmills and onsite
solar panels, and recycling stations for all types of
materials have replaced bins on the office floors.
Mountain view from the top
of our crafting facility in Lamphun